Cette page a été traduite automatiquement.
Merci de bien vouloir compléter un sondage de 1 minute concernant la qualité de cette traduction.
Optimiser le contrôle de couple d'un moteur PMSM avec défluxage en utilisant la calibration basée sur des modèles
Par Dakai Hu, MathWorks
La calibration des moteurs synchrones à aimants permanents (PMSM) est une étape indispensable dans le design de commandes d'entraînement de traction électrique haute performance. Traditionnellement, le processus de calibration implique des tests approfondis au dynamomètre (dyno) et le traitement des données ; sa précision dépend en grande partie de l'expertise de l'ingénieur en calibration.
La calibration basée sur des modèles standardise le processus de calibration PMSM, réduit les tests inutiles et génère des résultats cohérents. Il s’agit d’un flux de travail automatisé et éprouvé qui utilise la modélisation statistique et l’optimisation numérique pour calibrer de manière optimale les systèmes non linéaires complexes. Il peut être utilisé dans une large gamme d'applications et est bien connu pour être adopté dans la calibration du contrôle des moteurs à combustion interne. Lorsqu'il est appliqué à la calibration du contrôle des moteurs électriques, le workflow de calibration basé sur des modèles peut aider les ingénieurs en contrôle moteurs à obtenir un contrôle optimal du couple et du défluxage pour les PMSM.
Caractérisation et calibration PMSM : défis et exigences
Les PMSM se distinguent des autres types de moteurs électriques par leur rendement élevé et leur densité de couple. Cela est dû au fait que les aimants permanents à l’intérieur de la machine peuvent générer un flux magnétique important dans l’entrefer sans excitation externe. Cette caractéristique particulière fait d'un PMSM un excellent candidat pour les applications d'entraînement de moteur avec et sans traction.
La plupart des applications PMSM sans traction nécessitent uniquement que la machine fonctionne dans la région de couple constant, où son schéma de contrôle est relativement simple. Le contrôle PMSM de traction, en plus d'une réponse dynamique rapide, nécessite également une sortie de couple précise et un fonctionnement sur une large plage de puissance et de vitesse constante. Pour atteindre ces objectifs de contrôle, notamment dans un véhicule électrique ou hybride électrique, le PMSM de traction doit fonctionner dans la zone de défluxage où des compromis doivent être faits entre le couple, la vitesse et l'efficacité.
Une grande partie du design d’un algorithme de contrôle de défluxage haute performance consiste à calibrer les tables de recherche de contrôle de défluxage. Avant de générer les données du tableau, des tests de caractérisation PMSM doivent souvent être effectués soit en utilisant une configuration dyno ou via un outil FEA comme ANSYS Maxwell ou JSOL JMAG.
Après les tests de caractérisation du PMSM, des tableaux de couplage de flux et de couples mesurés à différents points de fonctionnement de courant et de vitesse peuvent être obtenus. Ici, nous devons distinguer la caractérisation du PMSM de la calibration. La caractérisation du PMSM implique la réalisation d'une série de tests soit sur un banc d'essai, soit à l'aide d'un outil FEA, dans le but d'extraire des informations importantes sur la machine, telles que le couplage de flux et le couple. La calibration du contrôle PMSM implique le calcul des tables de recherche du contrôleur qui généreront un couple maximal ou une efficacité optimale à différents points de fonctionnement. Le processus de calibration du contrôle se produit généralement après la caractérisation du PMSM. Les deux processus sont nécessaires pour un design de contrôle de PMSM haute performance.
Le workflow de calibration basé sur des modèles
Lorsqu'il est appliqué à la calibration du contrôle de PMSM, le workflow de calibration basé sur des modèles comporte généralement quatre étapes (Figure 1) :
- Designer l’expérience pour la caractérisation.
- Prétraiter l’ensemble de données de caractérisation du PMSM.
- Ajuster les modèles de caractérisation du PMSM.
- Optimiser les données de la table de recherche du contrôleur du PMSM.
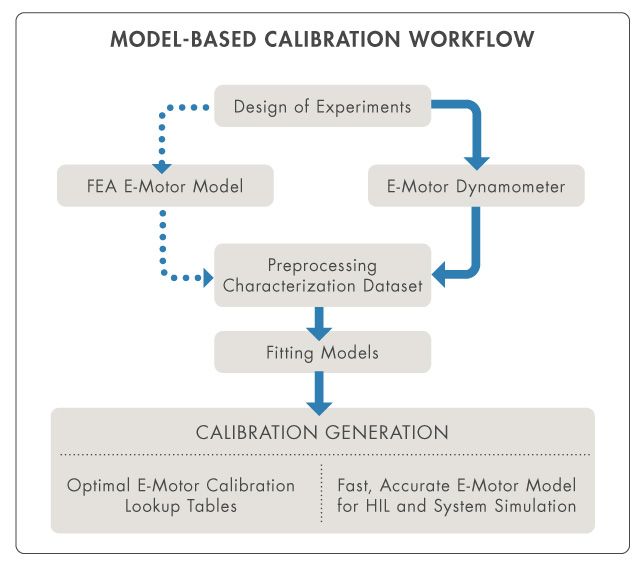
Figure 1. Workflow de calibration basé sur un modèle pour la calibration du contrôle de PMSM.
1. Designer l'expérience pour la caractérisation
La caractérisation factorielle complète sur un banc d'essai physique est un peu efficace car elle augmente le temps d'expérience, le coût et la maintenance. Dans la calibration basée sur des modèles, des points de fonctionnement statistiquement espacés sont proposés comme points de test. Que l'expérience soit réalisée sur un banc d'essai physique ou dans un environnement FEA, les points de test générés d'id et d'iq actuels seront donnés sous forme de commandes de contrôle et la vitesse du PMSM sera régulée par la machine dyno ou définie dans l'outil FEA. L'utilisation d'un dyno virtuel nécessite un modèle de FEA de PMSM détaillé. Cependant, une fois le modèle créé, il peut être testé sur un ensemble plus complet de points de fonctionnement sans entraîner de coûts supplémentaires.
2. Prétraiter l'ensemble de données de caractérisation du PMSM
Lors de la caractérisation du PMSM, les données de couple et de couplage de flux d'axe dq sont soit mesurées directement sur un dyno, soit dérivées d'un outil FEA pour chaque point de fonctionnement d'id, iq et vitesse. Après caractérisation, l'ensemble de données est réorganisé par contours de couple et pas de vitesse, et chaque variable (par exemple, le couple) est stockée dans un format à colonne unique, qui est ensuite importé dans Model-Based Calibration Toolbox™ (Figure 2). Si nécessaire, une analyse supplémentaire peut être effectuée pour supprimer les données aberrantes. Les valeurs aberrantes sont courantes lors des tests physiques en raison du bruit et des erreurs de mesure.
3. Ajuster des modèles de caractérisation du PMSM
L'ajustement du modèle est un élément crucial du workflow de calibration basé sur des modèles. (Notez que les modèles mentionnés dans cet article ne sont pas des modèles de moteurs ou de contrôleurs électriques ; ce sont des modèles statistiques dans lesquels des fonctions telles que la régression de processus gaussien ou la fonction de base radiale représentent la relation entre les variables dans l'ensemble de données importé.) Plus précisément, deux ensembles de modèles sont créés : iq en fonction de l'id et du couple, et la marge de tension en fonction de l'id et du couple. Chacun est modélisé sur un ensemble commun de vitesses de moteur. Ces vitesses sont utilisées comme points d’arrêt pour la table de recherche du contrôleur final. La figure 3 montre les modèles regroupés par deux points de fonctionnement de vitesse : 1 000 tr/min et 5 000 tr/min.

Figure 3. Exemples de modèles de marge Iq et de marge de tension (delta_vs) à différents points de fonctionnement de vitesse.
Les modèles de marge de tension et de Iq varient en fonction des points de fonctionnement de la vitesse, car la vitesse peut affecter directement la limite de fonctionnement. Il est impossible de représenter exactement la limite de fonctionnement à partir d’un nombre fini de points de données caractérisés. Les limites de fonctionnement réelles du PMSM étalonné sont souvent imposées par des facteurs limitatifs externes tels que la limite thermique du système d'entraînement et le niveau de tension du bus CC de l'onduleur.
Dans la calibration basée sur des modèles, les limites de fonctionnement des modèles ajustés sont approximées par les enveloppes convexes entourant l'ensemble de données, comme illustré par les bords des surfaces colorées dans la figure 3. Ces limites sont importantes pour l’étape 4 du workflow de calibration, car elles sont utilisées comme contraintes pour le problème d’optimisation.
4. Optimiser les données de la table de recherche du contrôleur du PMSM
Dans la calibration basée sur des modèles, le processus d'exécution des routines d'optimisation et de génération des tables de recherche de calibration finales est effectué à l'aide de CAGE, l'outil de génération de calibration de Model-Based Calibration Toolbox. Dans CAGE, les modèles de l’étape 3 sont utilisés soit pour des modèles de fonctions objectives, soit comme contraintes. Par exemple, les modèles de marge de tension sont utilisés comme contraintes de tension à différentes vitesses pour garantir que la tension de modulation globale ne dépasse pas le maximum imposé par la tension du bus CC. En plus des contraintes, des objectifs simples ou multiples peuvent également être définis sur la base de ces modèles ajustés.
Un objectif commun pour un contrôle optimisé du défluxage est de maximiser l'efficacité du PMSM tout en atteignant le couple requis. Ceci est réalisé en définissant le couple par ampère (TPA) comme cible pour maximiser et appliquer simultanément les contraintes de courant et de tension. Le résultat est une zone de fonctionnement optimisée qui couvre le couple maximal par ampère (MTPA), le couple maximal par volt (MPTV) et les points de fonctionnement intermédiaires.
La figure 4 montre comment un point d’opération optimisé dans la table de recherche est obtenu grâce au processus CAGE. Les zones ombrées bleu clair et jaune représentent les contraintes de courant et de tension correspondantes à un point de fonctionnement de vitesse spécifique, la zone verte étant la région viable satisfaisant les deux contraintes. Le contour de couple dans le graphique représente une exigence de couple spécifique. Pour obtenir un contrôle d'efficacité maximal pour le PMSM, l'optimiseur de CAGE effectue une recherche le long du contour de couple à l'intérieur de la région viable pour trouver un point qui maximise la cible TPA. Par conséquent, dans l’exemple illustré à la figure 4, le point A sera choisi comme optimal. Les autres points de table de recherche optimisés de la figure 4 sont calculés par la même routine dans CAGE.
Vous pouvez accélérer la routine d'optimisation décrite ci-dessus en l'exécutant avec Parallel Computing Toolbox™. Avec le calcul parallèle activé, l'ensemble du workflow converge en moins de 10 minutes sur un PC classique à quatre cœurs.
Après avoir exécuté la routine d'optimisation, vous pouvez remplir les tables de recherche de calibration finales avec les résultats d'optimisation via diverses méthodes de remplissage, telles que l'interpolation ou le découpage. En théorie, vous pouvez choisir n'importe quel point d'arrêt de couple et de vitesse pour la table de recherche, mais un choix courant de points d'arrêt pour le couple est le pourcentage du couple maximal. Le choix du pourcentage de couple par rapport au couple maximal réalisable plutôt que des valeurs de couple absolues garantit que l'ensemble de la table de recherche peut être rempli avec des résultats d'optimisation valides (Figure 5).

Figure 5. Tables de calibration d’id et d’iq optimisées avec défluxage inclus.
Extension du workflow
Cet article couvre le workflow de calibration basé sur des modèles de base pour la génération de tables de recherche de contrôle de couple de PMSM optimales avec défluxage. L'exemple décrit dans l'article est basé sur des tables de contrôle à défluxage où la commande de couple, la vitesse et éventuellement la tension du bus CC sont des entrées.
Pour un algorithme qui utilise la commande de couple et le couplage de flux maximum comme entrées dans ses tables de recherche, le workflow est le même, uniquement avec des modèles de fonction légèrement différents. De plus, si votre application nécessite une calibration plus précise et plus affinée, vous pouvez prendre en compte davantage de variables, telles que la chute de tension de l'onduleur, la perte de noyau, la résistance CA et le vent ou le frottement, lors de l'ajustement du modèle et du processus CAGE.
Publié en 2020